
Update
Verifying the pool CFD model
6th January, 2022
A recap on the first stage – developing the CFD pool model, where we completed the following:
- procurement and training on the Autodesk generic CFD software
- generation of a working model, with a steady state flow simulation and mapped velocities
- a transient simulation with the introduction of dye at each of the inlets
It was then essential for us to verify that our results were both robust and repeatable. We have available a library of dye test data that would assist this verification process, however we wanted to push this further! The pool that we had modelled was based on a local 25m competition pool, one that we had designed and specified. With the support of North Tyneside Council, we ran a real life dye test on the pool itself in order to verify our model.
The process exposed some weaknesses in our first model which would require further interrogation, research and refinement. The iterative process demanded a huge amount of man hours, significant hardware resource to handle the data being produced and additional technical support from Autodesk, to hone in on the right solution.
This was a significant learning process that threw up many new challenges along the way. The correct diffusion coefficient, turbulence model, mesh density and advection approach, to name but a few were all thoroughly reviewed. All of which play a key role in defining pool water distribution and subsequently in developing a robust and accurate model.
We now had a transient simulation pool tank CFD model, thoroughly researched, refined and verified in practice.
Results from the dye test after 10 and 20 minutes showing how the dye spreads throughout the pool.
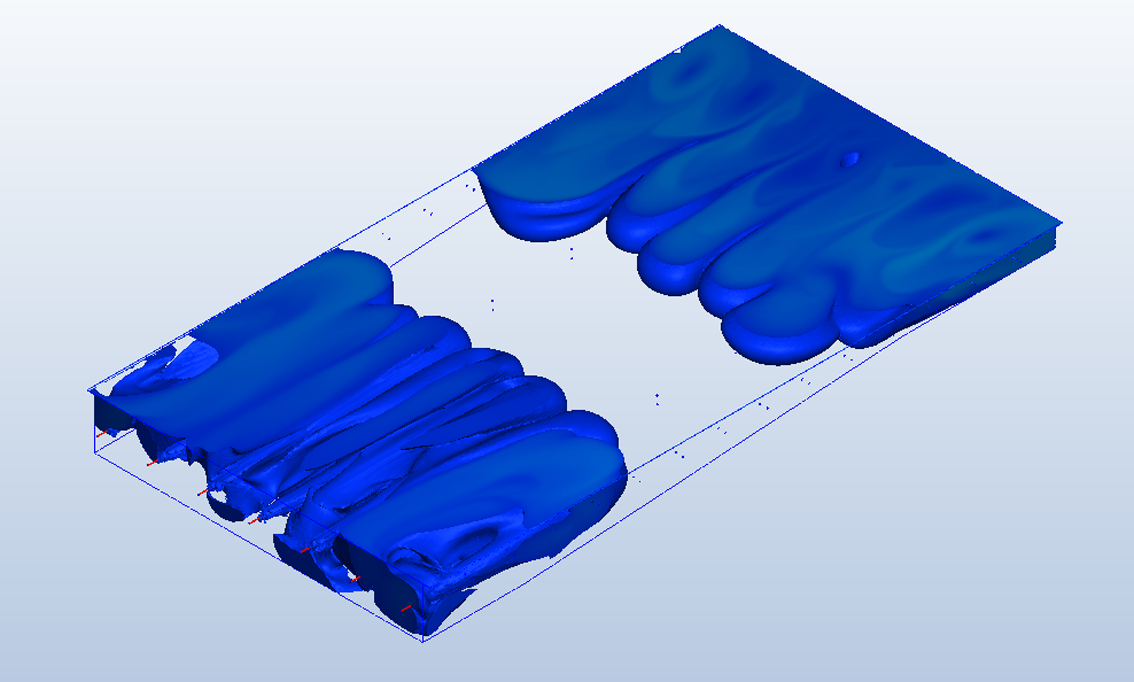
